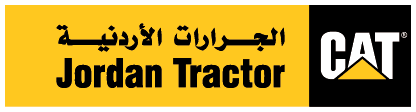
R1700
When it came time to redesign the Cat® R1700 Underground Loader, the goal was simple: add value, power and performance, and keep safety at the core. And we succeeded. With each cycle, the R1700 hauls 20% more material than its predecessor and is highly aggressive in the pile. It loads, climbs, hauls and dumps faster. And it’s factory ready for the latest technologies, including fully autonomous haulage, which takes safety and efficiency to a new level. The R1700 is infused with features to keep people safe. It offers three engine emission options, including one that meets Stage V standards, and can be tailored to your mine’s ventilation requirements. A clean-sheet redesign, the R1700 loader leverages engineering talent from across Caterpillar to create the next generation of productive underground loading.
Engine Model
Cat® C13
Engine Power - Stage V Engine - ISO 14396:2002
345 HP
Engine Power - Tier 3 Engine - ISO 14396:2002
361 HP
Specification
Value
Engine Model
Cat® C13
Engine Power - Stage V Engine - ISO 14396:2002
345 HP
Engine Power - Tier 3 Engine - ISO 14396:2002
361 HP
Engine Power - VR Engine - ISO 14396:2002
361 HP
Note (1)
Power ratings apply at a rated speed of 1,800 rpm for LRCs (VR and Tier 3/Stage IIIA) engines when tested under the reference conditions for the specified standard.
Note (2)
Power ratings apply at a rated speed of 2,050 rpm for HRC (Stage V) engine when tested under the reference conditions for the specified standard.
Note (3)
All rating conditions are based on ISO/TR14396, inlet air standard conditions with a total barometric pressure of 100 kPa (29.5 in Hg), with a vapor pressure of 1 kPa (0.295 in Hg), and 25° C (77° F). Performance measured using fuel to EPA specifications in 40 CFR Part 1065 and EU specifications in Directive 97/68/EC with a density of 0.845-0.850 kg/L @ 15° C (59° F) and fuel inlet temperature 40° C (104° F).
Note (4)
No engine derating required up to 2895 m (9,500 ft) altitude for Stage V engines, 3505 m (11,500 ft) altitude for Tier 3/Stage IIIA engines, and 3200 m (10,500 ft) for Tier 2/Stage II VR engines.
Note (5)
Optional Ventilation Reduction package available.
Note (6)
Optional engine with emissions equivalent to Tier 3 and Stage IIIA is also available.
Note (7)
Optional engine meeting the U.S. EPA Tier 4 Final and EU Stage V emission standards is also available.
Specification
Value
Nominal Payload Capacity
33069 lb
Gross Machine Mass - Loaded
138316 lb
Static Tipping Load - Straight Ahead - Lift Arms Horizontal
83218 lb
Static Tipping Load - Full Turn - Lift Arms Horizontal
69635 lb
Breakout Force - Lift and Tilt
53330 lb
Specification
Value
Operating Mass*
95189 lb
Operating Mass* - Front Axle
38358 lb
Operating Mass* - Rear Axle
56831 lb
Operating Mass + Rated Payload*
128258 lb
Operating Mass + Rated Payload* - Front Axle
91412 lb
Operating Mass + Rated Payload* - Rear Axle
36846 lb
Note
*Calculated weights.
Specification
Value
Forward - 1
3 mile/h
Forward - 2
5.7 mile/h
Forward - 3
10.2 mile/h
Forward - 4
17.9 mile/h
Reverse - 1
3.7 mile/h
Reverse - 2
6.5 mile/h
Reverse - 3
11.6 mile/h
Reverse - 4
20.2 mile/h
Specification
Value
Raise
6.8 s
Dump
3.3 s
Lower, Empty, Float Down
2.9 s
Total Cycle Time
13.2 s
Specification
Value
Bucket Capacities
5.7-8.6 m³ (7.5-11.2 yd³)
Dump Bucket - 1 - Standard Bucket
7.5 yd³
Dump Bucket - 2
8 yd³
Dump Bucket - 3
8.6 yd³
Dump Bucket - 4
9.4 yd³
Dump Bucket - 5
9.8 yd³
Dump Bucket - 6
10.5 yd³
Light Material Bucket
11.2 yd³
Ejector Bucket
7.6 yd³
Bolt Together Bucket (1)
8.9 yd³
Bolt Together Bucket (2)
9.8 yd³
Specification
Value
Outside Clearance Radius
272 in
Inner Clearance Radius
123.5 in
Axle Oscillation
8°
Articulation Angle
44°
Specification
Value
Tire Size
26.5R25
Specification
Value
Cooling System
19.8 gal (US)
Engine Crankcase
9.8 gal (US)
Hydraulic Tank
35.7 gal (US)
Specification
Value
Fuel System
128.4 gal (US)
DEF Tank
7.1 gal (US)
Front Differential and Final Drive
39 gal (US)
Rear Differential and Final Drive
37.2 gal (US)
Transmission
14.2 gal (US)
- Improvements in visibility, with lighting and camera coverage, including optional reverse operation camera with color display, multiple windshield wipers, and standardized LED lights that provide illumination to the front and rear.
- Factory-ready for fire suppression, dedicated canister area estate and multiple fire suppression activation points, including from within the cab.
- Improved access and egress with anti-slip tread on all walking surfaces, newly redesigned handrail system with full coverage and dual secondary emergency exits.
- Operator Present System, which protects the machine and operator from uncontrolled machine movements, with hydraulic system neutralization and door sensor.
- Safer service with service area located on cold side of engine, thermal protection on aftertreatment components, integrated lock-out/tag-out points, front linkage pins for locking the lift arms in place, and bolt-on tow hooks.
- Completely redesigned cab with more space, with operator seated lower to improve ride quality and head room; adjustable padding for the operator’s knees; and additional foot-space during pedal operation.
- Climate control standard with pressurized enclosed option; all new HVAC coverage with improved airflow, greater defrosting coverage and reduced noise levels.
- Improved ergonomics on all controls, easy-to-use joystick controls, and an isolation-mounted cab to reduce vibration transfer to the operator.
- Four corner oil-cooled braking system, which provides excellent control.
- Oscillating rear axle, which ensures four-wheel ground contact for maximum traction and stability at all times, plus a no-spin rear differential that reduces tire wear and maximizes traction in uneven terrain.
- Fast cycle times thanks to integrated ride control system, which gives operators confidence to travel at speeds above 5 km/h (3 mph) during load and carry operations.
- Hydraulic system that provides significantly more breakout force during digging, and that gives the machine faster dumping times at the other end of the cycle.
- Repositioned front linkage cylinders for better mechanical lift.
- Features that deliver excellent responsiveness, such as Auto Dig, which automates loading of the bucket; and pilot-controlled steering system to provide more acute feel in tight spaces.
- Hydraulically actuated auto retarding, which improves cycle times as operators gain confidence and become more comfortable on downhill grades at faster speeds.
- C13 engine that is larger than previous model for more power and performance, with 6-cylinder configuration that is turbo-charged and air-to-air aftercooled.
- New lock-up clutch torque converter that engages automatically as the machine shifts into second gear.
- Mechanically Actuated, Electronic Unit Injection (MEUI™) high-pressure, direct injection fuel system, which electronically monitors operator demands and sensor inputs to optimize engine performance and fuel combustion.
- State-of-the-art hydraulic system, which uses on-demand piston pumps for durability, higher pressures and overall system efficiency, and provides full system pressure for operator while the engine is at idle.
- Newly resized Cat transmission governed by APECS software, which allows the transmission to comfortably shift under higher torque conditions and makes it possible for the machine to climb grades more quickly by reducing lost momentum between shifts.
- Newly patented bucket design that offers load path management for long wear life, increased throat angle for easier loading in rock, improved tire coverage for cleanup and tire protection, added strength to match improved breakout force, and added stiffness to inside torque tube for torsional rigidity.
- 10 bucket options, including six dump bucket sizes, one light material bucket, one ejector bucket option and two bolt-together options — all designed and manufactured to match their performance capabilities.
- Three types of Ground Engaging Tools (GET) available: modular weld-on, which deliver welded part reliability; Bolt-On-Half-Arrow (BOHA), which offer more wear material and feature a bolt-on design that enables fast and easy removal and replacement; and the Durilock Lip Shroud system, featuring hammerless installation and maintenance-free retention of GET, with three interchangeable shroud styles.
- Cat Bucket Pro App, which provides real-time data on GET performance to help you plan maintenance, manage inventory and know cost-per-ton.
- Front frame section with four-plate design that offers new, fully integrated front axle support casting that absorbs greater impact, vibration and tram loads that come with the growth of the machine capacity and weight.
- Increased axle housing thickness for abrasion protection and corrosion resistance.
- Visibly stronger lift arms with additional steel thicknesses, to ensure extreme loads encountered during loading and tramming are efficiently dissipated for long service life.
- Frame, powertrain, engine and components that are built to be rebuilt.
- ECMs located in single, air-cooled and sealed box located on the service platform of the machine, providing clean, simplified electrical routings throughout the machine and greatly improved access and convenience for service personnel.
- Redesigned hitch with simplified hydraulic routings and more space for technicians to work and clean.
- Modular components that can be removed from the machine and slotted back into place as a single unit, allowing the machine to get back into service much more quickly.
- Improved service access, with swing-open radiator guard, and filter and key service tasks grouped into centralized service section with oil coolers and batteries located just below.
- Fuel tank that bolts in to the frame, allowing it to be easily cleaned or replaced if damaged as it bolts in to the frame.
- Factory-ready for remote operation and can be equipped with the industry-proven Cat® MineStar™ Command for underground, which offers line-of-sight remote control; teleremote operation; co-pilot, which requires only directional input from the operator; and fully autonomous operation.
- High-resolution dash displays with 11 language options for access to real-time system information.
- In-cab health monitoring visible on the digital display and monitored through the Cat Product Link™ Elite (PLE) system, including integrated MineStar Health offerings that enable proactive maintenance services and predictive equipment analysis.
- Optional MineStar Fleet for underground, which provides real-time visibility to cycle time, payload, machine position and other key operational parameters.
- Optional MineStar Detect, which uses a proximity detection system coupled with a revolutionary communications and tracking network to prevent incidents and track people and machines in real time.
- Three engine emission options, including EU Stage V, Tier 2 and Tier 3, which reduce emission of NOx and particulates.
- Ongoing research and development into engine compatibility with diesel fuel blended with lower-carbon intensity fuels such as biofuels and renewable fuels, plus power options like electrification.
- Optional Ventilation Reduction (VR) Package, which incorporates selective engine hardware and software to reduce diesel particulate matter in the engine exhaust.
- Cat Rebuild and Cat Reman programs, which preserve raw materials, conserve energy and reduce emissions.
- Retrofits and upgrades for older machines — to incorporate efficiency improvements and emission reductions, and to keep them in production longer to conserve energy and minimize the need for raw materials.