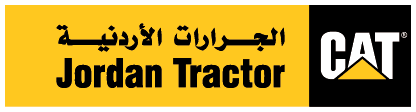
789
The Cat® 789 Mining Truck is the most popular 193-tonne (213-ton) truck in the mining industry — and for good reason. Developed specifically for high-production mining applications, the 789 simply does its job, no matter the application or conditions. It continues a legacy of durability and reliability while meeting emission standards for any location in the world. It uses less fuel, has expanded safety options and reduces maintenance downtime. It offers fast speed on grade and a high production capability thanks to a payload advantage over the competition. More than 30 new features improve performance and keep operators safe, comfortable and in control. The 789 offers the lowest cost per ton in its size class and high reliability — reducing overall owning and operating costs.
Gross Power - SAE J1995:2014
2,100 HP
Engine Model
Cat® 3516E
Net Power - SAE J1349:2011
1,975 HP
Specification
Value
Gross Power - SAE J1995:2014
2,100 HP
Engine Model
Cat® 3516E
Net Power - SAE J1349:2011
1,975 HP
Rated Speed
1,650 r/min
Emissions Rating
Fuel Optimized
Bore
6.7 in
Stroke
8.5 in
Displacement
4,766 in³
Note (1)
Net Power advertised is the power available at the flywheel when the engine is equipped with air intake system, exhaust system, and alternator.
Note (2)
Optional 1417 kW / 1,900 HP engine rating.
Note (3)
U.S. EPA Tier 4 Final / EU Stage V optional engine available for applicable markets.
Specification
Value
Rated Gross Machine Weight
715,000 lb
Body Weight
60,406 lb
Note (1)
Consult your tire manufacturer for maximum tire load
Note (2)
Chassis weight with full fuel and fluids, standard and mandatory attachments, hoist, body mounting group, rims, and tires.
Nominal Rated Payload
213 ton (US)
Specification
Value
Front Axle - Empty
50%
Rear Axle - Loaded
67%
Rear Axle - Empty
50%
Front Axle - Loaded
33%
Specification
Value
Planetary Ratio
10.83:1
Total Reduction Ratio
25.46:1
Type
Double reduction, planetary with full floating axles
Differential Ratio
2.35:1
Specification
Value
Forward - 1
7.8 mile/h
Forward - 2
10.6 mile/h
Forward - 3
14.4 mile/h
Forward - 4
19.4 mile/h
Forward - 5
26.3 mile/h
Forward - 6
35.5 mile/h
Reverse
7.3 mile/h
Top Speed - Loaded
35.5 mile/h
Specification
Value
Standard Tires
37 R57
Optional Tires
40 R57
Optional Tire
42/90 R57
Rims
29” x 57” Rims
Note (1)
Quick Change Rims optional
Note (2)
Caterpillar recommends the customer evaluate all job conditions and consult tire manufacturer for proper tire selection and TKPH (TMPH) capabilities.
Specification
Value
Service Brakes
Four-Corner, Wet Disc, Oil Cooled, Hydraulically Actuated
Front Wet Disc Brake Surface Area
12,662 in²
Rear - Wet Disc Brake Surface Area
20,861 in²
Standards
(Service and Secondary) ISO 3450:2011
Parking Brake
Four-corner, Multi-disc, Spring applied, Hydraulically Released
Specification
Value
Struck
77 m3(101 yd3)
Heaped (SAE 2:1)*
143 m3(187 yd2)
Note (1)
Consult your local Cat dealer for body recommendations
Specification
Value
Type
Twin, two-stage hydraulic cylinders with snubbing valve.
Pump Flow - High Idle
106.5 gal/min
Relief Valve Setting - Raise
2,749 psi
Body Raise Time - High Idle
14 s
Body Lower Time - Float
16 s
Specification
Value
Type
Self-contained nitrogen/oil cylinders, pin-to-pin mounting, top and bottom double shear clevis attachments
Effective Cylinder Stroke - Front
4.12 in
Effective Cylinder Stroke - Rear
3.67 in
Rear axle - Oscillation
+/- 5 degrees
Specification
Value
Fuel Tank - Standard
550 gal (US)
Fuel Tank
1000 gal (US)
Fuel Tank (Tier 4)
55 gal (US)
Diesel Exhaust Fluid Tank
62 gal (US)
Cooling System
180 gal (US)
Crankcase
77 gal (US)
Front Wheels - Each
5.8 gal (US)
Differentials
161 gal (US)
Steering System
42 gal (US)
Steering System - Includes Tank
46 gal (US)
Brake Hoist System
169 gal (US)
Brake Hoist System - Includes Tank
347 gal (US)
Torque Converter - Transmission System - Including Sump
55 gal (US)
Specification
Value
Air Conditioning
(HFC - 134A refrigerant) 24,500 Btu/hr
Heater / Defroster
33,300 Btu/h
ROPS Standards (1)
The operator sound pressure level, 77 dB(A) with direct drive and 75 dB(A) with optional clutch, tested to ISO 6396:2008.
ROPS Standards (2)
ROPS (Rollover Protective Structure) meets ISO 3471:2008 for Operator and ISO 13459:2012 for Trainer.
FOPS Standards
FOPS (Falling Objects Protective Structure) meets ISO 3449:2005 Level II for Operator and ISO 13459:2012 Level II for Trainer.
Specification
Value
Steer Angle
36.07 °
Steering Standards
ISO 5010:2007
Specification
Value
Height - Top of ROPS
5550 mm
Overall Body Length
12945 mm
Inside Body Length
8730 mm
Overall Length
12970 mm
Wheel Base
57000 mm
Rear Axle - Tail
3856 mm
Ground Clearance
1304 mm
Dump Clearance
1585 mm
Loading Height - Empty
6147 mm
Rear Sidewall Height
1010 mm
Inside Body Depth - Maximum
3075 mm
Overall Height - Body Raised
11534 mm
Operating Width
7822 mm
Centerline Front Tire Width
5410 mm
Engine Guard Clearance
1290 mm
Overall Canopy Width
7769 mm
Outside Body Width
7123 mm
Inside Body Width
6920 mm
Front Canopy Height
6739 mm
Rear Axle - Clearance
1263 mm
Centerline of Rear Dual Tire Width
4695 mm
Overall Tire Width
7120 mm
- The 789 delivers a faster speed on grade than competitive trucks thanks to the efficient 3516E 16-cylinder engine and mechanical drivetrain.
- Expanded tire options allow mines to take advantage of higher speeds, particularly in flat, long-haul, high-speed applications.
- The Advanced Power Electronic Control Strategy (APECS) enables faster cycle times and faster acceleration thanks to more continuous torque and rimpull.
- The 789 has an empty machine weight advantage, allowing it to haul more with every load, delivering a cost per ton advantage over competitive trucks.
- Productivity-enhancing features such as Hill Start Assist with Anti-Rollback, Enhanced Traction Control, Dynamic Stability Control (DSC), Anti-lock Brake System (ABS), Machine Speed Limiting and Cruise Control improve machine responsiveness and controllability while improving cycle times and reducing operator fatigue.
- Wide, slip-resistant surfaces and hand rails, plus an optional powered access ladder, improve access and egress.
- Superior control is delivered by a patented braking system that provides immediate, fade-resistant braking and retarding.
- Visibility is enhanced by wide-angle mirrors plus an optional 360-degree Surround View camera, which offers a bird’s-eye view.
- The Cat MineStar™ Object Detection system combines radar and camera systems to warn operators about light vehicles or stationary hazards within the immediate vicinity of their machines.
- The optional Driver Safety System alerts the operator if fatigue or distraction are detected.
- The cab provides 34% more operator space than D-Series models. It’s 17% wider and offers 11% more legroom and 19% more shoulder room.
- Controls, levers and switches are positioned for ease of use.
- With 40% less Sound Pressure Level (SPL), automated temperature control and cab filtration, operators enjoy a safer and more comfortable environment.
- A walkthrough cab with fully adjustable center console, easy-to-adjust seat and increased leg room make the cab ideal for operators of all sizes.
- The next generation seat is four-point-restraint ready and incorporates features like thigh tilt and extensions, air adjustable side and lumbar bolsters, and heated and cooled cushions.
- Higher resolution displays improve access to information. Machine data, controls and guidance information are consolidated onto two 10-inch screens.
- The optional Auto Hoist feature automatically raises the body and controls engine speed, simplifying operation and minimizing cycle times.
- Speed coaching gives operators real-time feedback on how to operate the truck to maximize its productivity.
- The payload monitoring system comes with more accurate measurements, providing immediate feedback to the operator.
- The new modular HVAC (heating, ventilation and air conditioning) system improves reliability and consolidates components so the entire system can be removed and replaced quickly.
- A modular radiator reduces engine removal and installation time and enables rebuilds to be completed off the truck.
- New remote flash and remote troubleshooting capabilities provide immediate access to the latest software updates and make it possible to troubleshoot the machine remotely.
- Time spent on regular maintenance procedures is reduced thanks to features such as extended service intervals; ground-level access to tanks, filters, drains and engine shutdown; easier access to daily service points as well as major components; a maintenance platform with access to the engine; and optional fast-fill service center.
- A 100% airless electric start option eliminates air system maintenance from the machine and improves uptime.
- The 789 frame uses a box-section design, incorporating two forgings and 21 castings in high-stress areas with deep penetrating and continuous wrap-around welds to resist damage from twisting loads without adding extra weight. The mild steel frame provides flexibility, durability and resistance to impact loads.
- Resiliently mounted to the main frame to reduce vibration and sound, the integral ROPS is designed as an extension of the truck frame.
- Component life is enhanced thanks to the standard rear-axle continuous filtration feature. Cleaner oil helps promote lubrication that leads to longer life
- The frame, powertrain, engine and components are built to be rebuilt — delivering multiple lives of like-new performance at a fraction-of-new price.
- Cat bodies are the best choice for the 789. They’re designed to be an integral part of the entire vehicle system, ensuring you achieve maximum chassis life.
- The High Performance (HP) body features a lightweight, simplified and durable design that provides complete front machine coverage and extended overhead protection.
- Available in several sizes, the MSD II body is ideal for mature mines with good operational and maintenance practices. It can be lined or unlined, with a site-specific body designed to maximize performance.
- Intended for tough applications including greenfield sites and contracting mines, the Dual Slope body provides excellent load retention, maintains a low center of gravity with optimum load distribution and reduces shock loading.
- The X Body incorporates the latest structural designs and offers more volume at a lower weight. It uses the Cat Mine Specific Design to create a body that is properly sized to meet the specific requirements of heavy-duty applications.
- The 789 is designed to use less fuel, which reduces engine emissions, and there is zero fuel burn during retarding. The Tier 4 Final engine reduces NOx and particulate matter.
- The Cat 3516E provides emission choices: fuel-optimized engine for less regulated countries or optional engine compliant to U.S. EPA Tier 4 Final / EU Stage V emissions standards.
- The 789 engine is compatible with diesel fuel blended with lower-carbon intensity fuels such as biofuels and renewable fuels.
- Features like oil renewal systems, continuous rear axle filtration, extended life filters and longer maintenance intervals decrease the amount of waste contributed to the environment.
- By rebuilding machines and components, the Cat Rebuild and Cat Reman programs preserve raw materials, conserve energy and reduce emissions.
- The Cat 3516E engine has proven its ability to deliver high power and reliability in the most demanding mining applications.
- The mechanical drive powertrain and power shift transmission provide unmatched efficiency and control on steep grades, in poor underfoot conditions and on haul roads with high rolling resistance.
- Application-specific capabilities are available for extreme ambient conditions and high-altitude applications.
- The 789 lets you select the tire offering that best matches your application, with a larger tire for flat, long, high-speed applications. The frame is designed to maintain the same turning diameter while accommodating larger tires.
- The 789 is available in two options to meet the emissions standards. The optional Tier 4 Final engine meets the strictest standards while the LRC engine is available in those countries that are less regulated.
- MineStar Fleet is a fleet monitoring system that can be used to measure, manage and maximize the overall hauling operation.
- Additional Detect offerings include Awareness, which can provide warnings and the in-cab Driver Safety System, which intervenes when it detects fatigue or distraction.
- Machine health and condition monitoring solutions enable a proactive approach to maintenance.