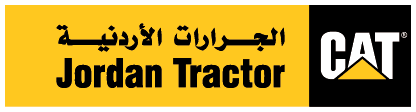

Available in stock
BF90.3 S4
The BF90.3 Bucket Crusher for excavator is the flagship Bucket Crusher produced and patented by MB in 2001. It became the first crusher bucket to be manufactured in the world. Today, it continues to be the most popular model for medium- to large-sized companies. It is designed to eliminate material friction in the loading phase and to resist even the most difficult on-site conditions. The Bucket Crusher BF90.3 is extremely compact and versatile. It has been improved and enhanced over the years to accommodate all crushing operations. Even in the harshest scenarios, the BF90.3 maintains its high level of performance, working with any type of inert material. The BF90.3 is suitable for excavators weighing over 46,300 pounds and has a load capacity of 1.17 cubic yards. It achieves a production rate from 16 cy/h to 55 cy/h, depending on the output adjustment.
Weight
7716 lbs
Load capacity
1.17 cy
Pressure
> 3,191 PSI
Oil flow
>48 <63 gal/min
Mouth opening width
36 in
Mouth opening height
21 in
Specification
Value
Weight
7716 lbs
Specification
Value
Load capacity
1.17 cy
Specification
Value
Pressure
> 3,191 PSI
Specification
Value
Oil flow
>48 <63 gal/min
Specification
Value
Mouth opening width
36 in
Specification
Value
Mouth opening height
21 in
From enormous job sites or small spaces to steep and uneven environments. Areas that are difficult to access, high temperatures, limitations tied to hourly production and hauling expences, are just a few of the challenges surrounding extraction activities.
In this situation, two key factors can change how profitable quarries and mines are. Reducing the logistic costs surrounding stationary recycling plants and reusing extracted materials, especially waste such as quarry scraps, is often a loss in the company's books.
Companies dealing with construction, road work repairs, demolitions, paving, and city and urban landscape redevelopments. When faced with leveling job sites, companies deal with high management costs and many critical issues aimed at protecting the environment.
The priority is managing the excavated material in an inexpensive way for the company and minimizing the impact on the community.
All companies that offer roadwork services – such as work on outer suburban arterial roads, industrial infrastructures, bike paths, bridges or historic downtown alleys - all have to face:
Site complications like highly populated or extremely isolated locations that aredifficult to access
While keeping in mind vibration, hauling and equipment transportation restrictions,
Moving waste material out of the job site,
Purchasing fill material,
Transporting supplies to and from the site
A successful construction site is subject to many variables: how professional and eco-friendly the companies involved are and their ability to stay on budget.
Other factors that weigh heavily on a job’s bidding price and need to be considered are material handling, hauling, and disposal expenses; add noise, vibration and dust emission restrictions to the equation and you have a logistic nightmare that can impact the surrounding residential area and ultimately, the environment.
It is now possible to process material on site, without affecting the area's residents daily routine and keeping it "green". This allows contractors to cut costs, recycle waste material, and increase profit while being eco-friendly. With actual advantages for both the company and the community.
All
Photos
Videos
360 View